For my GCSE DT coursework I was given the brief to build a product in the context of climate change, what started as a mere school project, soon became my passion project for the year. Below, is the cumulation of hundreds of hours (if not thousands) of research, designing, pitching and building.
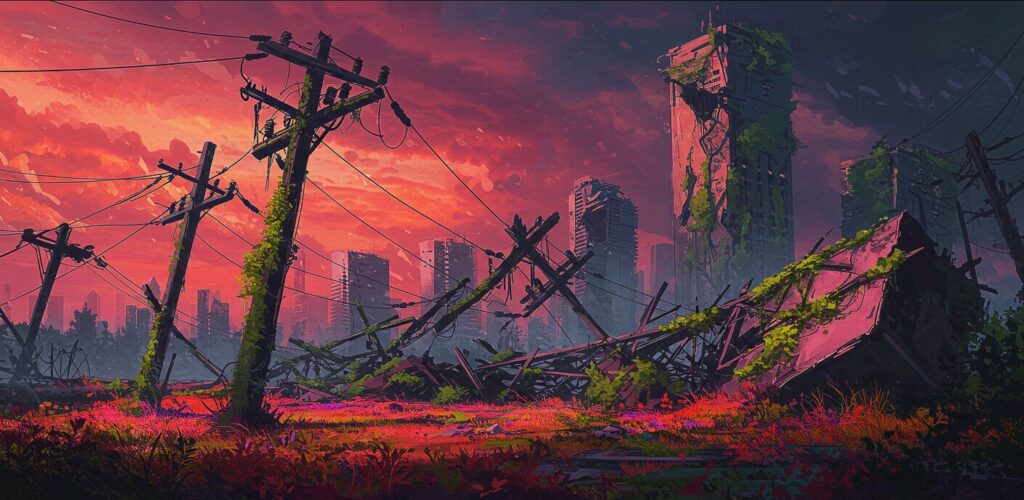
Initial spark
Having a long-standing passion for illumation/lighting (covered in hobbies section), I already knew I wanted to build a project that was focused on illumination.
When researching the effects of climate change, I came across the significant strain that our electrical grid was under due to the extreme conditions caused by climate change responsible for 83% of all power outages. I therefore decided to gear my product towards tackling power outages.
My product would have to be able to fulfill two main purposes: to charge essential devices and to provide enough light to illuminate rooms.
Diving into research
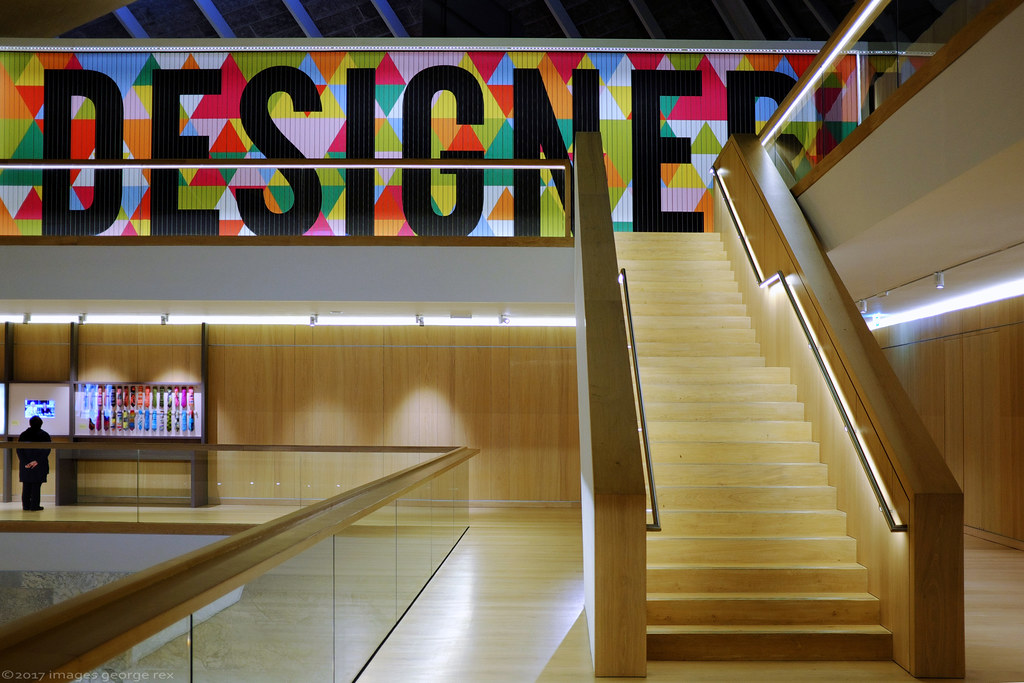
Good design starts with good research. From visiting the Design Museum to disassembling a high end torch, my product slowly began to come to life. After my research I decided on two main design decision to complement my two main functions. Bauhausian design and Ceiling bouncing.
The general consensus for the design of emergency products is that it should be tough and ugly. However, I had an alternate theory… What if making an emergency project stylish and sleek could make it more effective? Sounds counterintuitive, but that was my hypothesis. By having an attractive emergency lantern the client would be encouraged to position the product in the open, therefore improving its accessibility, giving it an edge over my competition. I therefore decided to implement Bauhausian elements into the design not only blending it into the modern home, but also being a nod to my client’s german heritage.
My research also uncovered a concept known as “Cieling Bouncing”, which quickly grew to the favourite part of my product. Cieling Bouncing is the idea that instead of diffusing light using a transclucent medium you shine the light on the cieling which reflects off of the white walls. This ingenious method pioneered by the photography industry allows for an even beam, a clean hidden light source and an elegant solution for my product.
Shaping the design
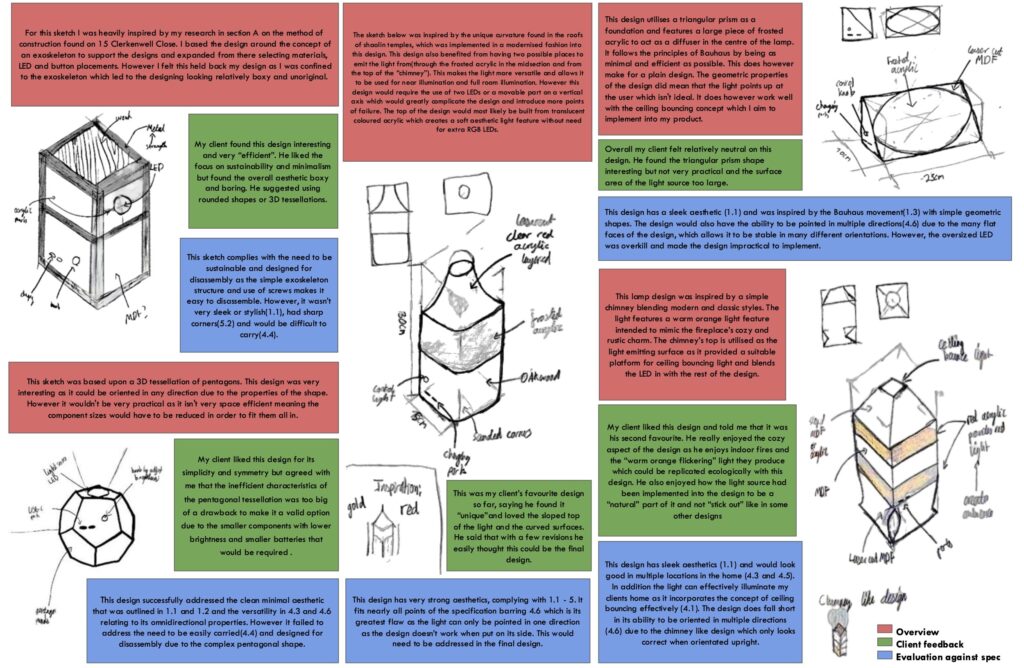
The design process thrives on iteration; exploring multiple prototypes is key. My initial concepts were far from the mark, resembling rugged fortresses rather than the sleek minimalist design I envisioned. It was only through a cycle of sketching, prototyping, and refining that I was able to move past these early failures and shape a design suitable for advancement (central).
The final design emerged as a rounded cube, crafted from wood with box joints for a clean, strong construction. I chose detachable magnetic legs for versatility and ease of use. At its heart lies the illuminating element: an acrylic structure that not only houses the light but also adds a layer of visual intrigue to the design improving an otherwise plain design.
Sustainability was also a driving force throughout the design process. This led me to incorporate a press-fit base, avoiding the use of glue to maintain repairability without sacrificing aesthetics. To further minimise environmental impact, I also created a detailed digital repair guide, accessed through a laser-cut QR code, eliminating the need for printed manuals and encouraging users to repair the product.
Building: Triumphs and Trials
The manufacturing phase presented a steep learning curve, particularly when it came to the woodwork. Cutting the box joints by hand proved far more challenging than anticipated; my initial attempts were, to put it mildly, imperfect. However, with persistent practice, my precision steadily increased. I meticulously filed each joint for a tight fit, using wood filler only sparingly to address any minor imperfections.
The detachable leg design also underwent significant iteration. The initial pin-and-box mechanism, while intended to be repairable, suffered from slight gaps that compromised the overall aesthetic. I ultimately replaced this with a friction-fit and magnetic system. This required painstaking sanding to achieve the precise tolerances needed for a secure, yet easily removable, connection. In the end the legs had turned out even better than I had anticipated.

Creating the acrylic centerpiece presented a unique engineering challenge. Its intricate geometry demanded a deep understanding of spatial relationships and the application of precise mathematical calculations to ensure seamless alignment of all components. The result, however, is a visually captivating central element.
The electronics presented their own complexities. The power source consists of standard 21700 batteries housed in a parallel case, connected with repurposed wires. A custom-machined brass pill and copper spacer, fabricated on a lathe, securely hold the high-performance Nichia 519A LEDs. To promote longevity and repairability, I laser-etched a QR code onto the device, providing direct access to a comprehensive repair guide. This reflects a commitment to minimizing electronic waste and extending the product’s lifespan.
The final stages involved meticulous finishing. The wood was sanded to a 240-grit finish, resulting in a smooth, tactile surface. Three coats of Teak oil were then applied to enhance the wood’s natural grain and provide a protective layer.
Reflection
Reflecting on the entire process, from initial concept to finished product, fills me with a sense of accomplishment. While countless improvements could still be made, I’m proud of what I created.
However, the most profound outcome wasn’t the object itself, but the personal growth I experienced. Each iteration of the design presented unique challenges, demanding creative solutions and pushing me beyond my comfort zone. From learning new woodworking techniques to unraveling the complexities of the acrylic form and the electronic components, I continuously expanded my skills and cultivated a mindset of constant learning.
The project became a testament to what can come if one can stick to a project for an extended period of time (something I usually struggle with.) This experience was without a doubt, one of the most valuable of my academic career.
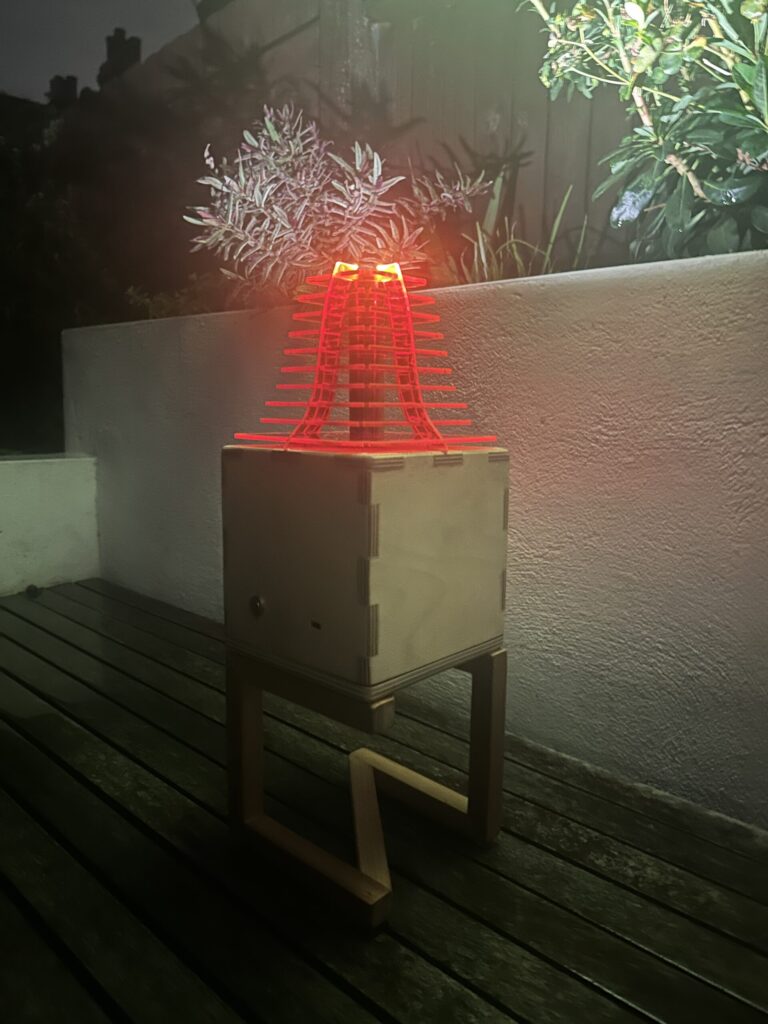
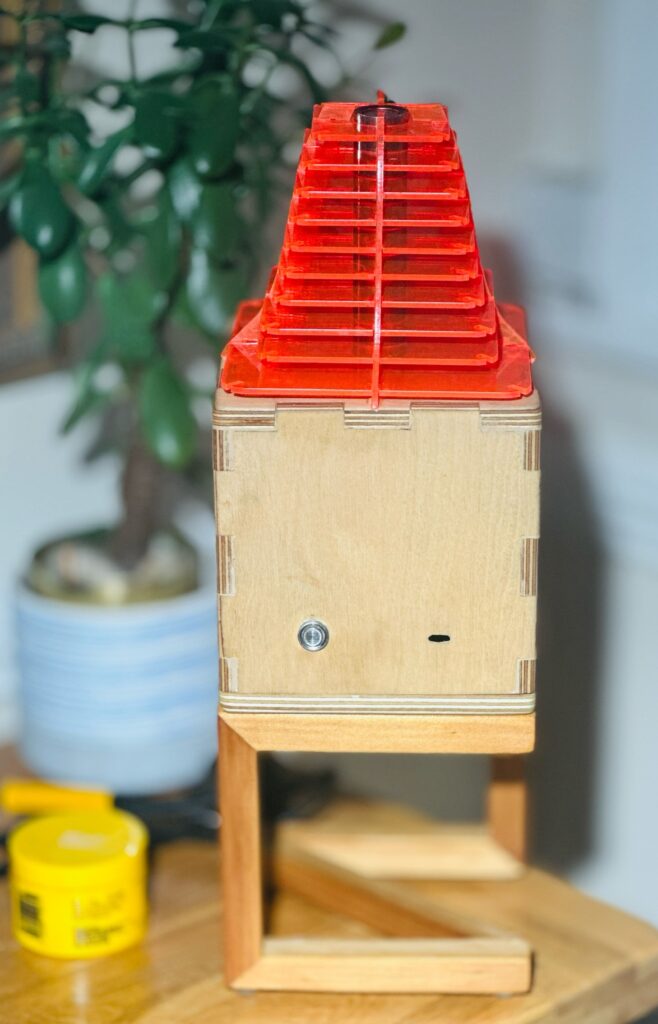
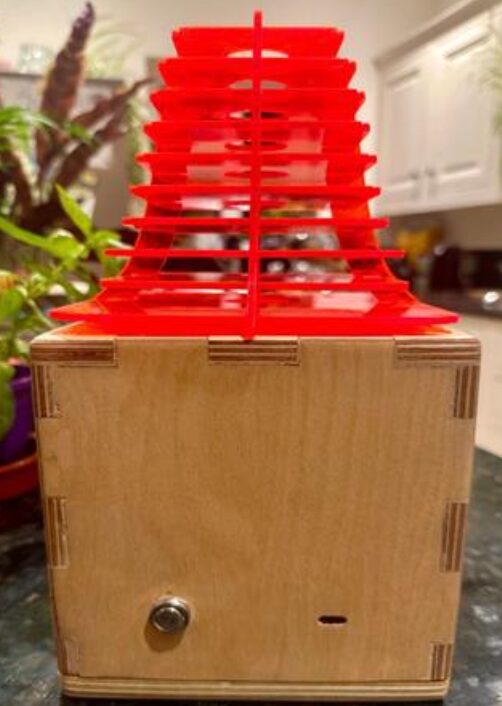
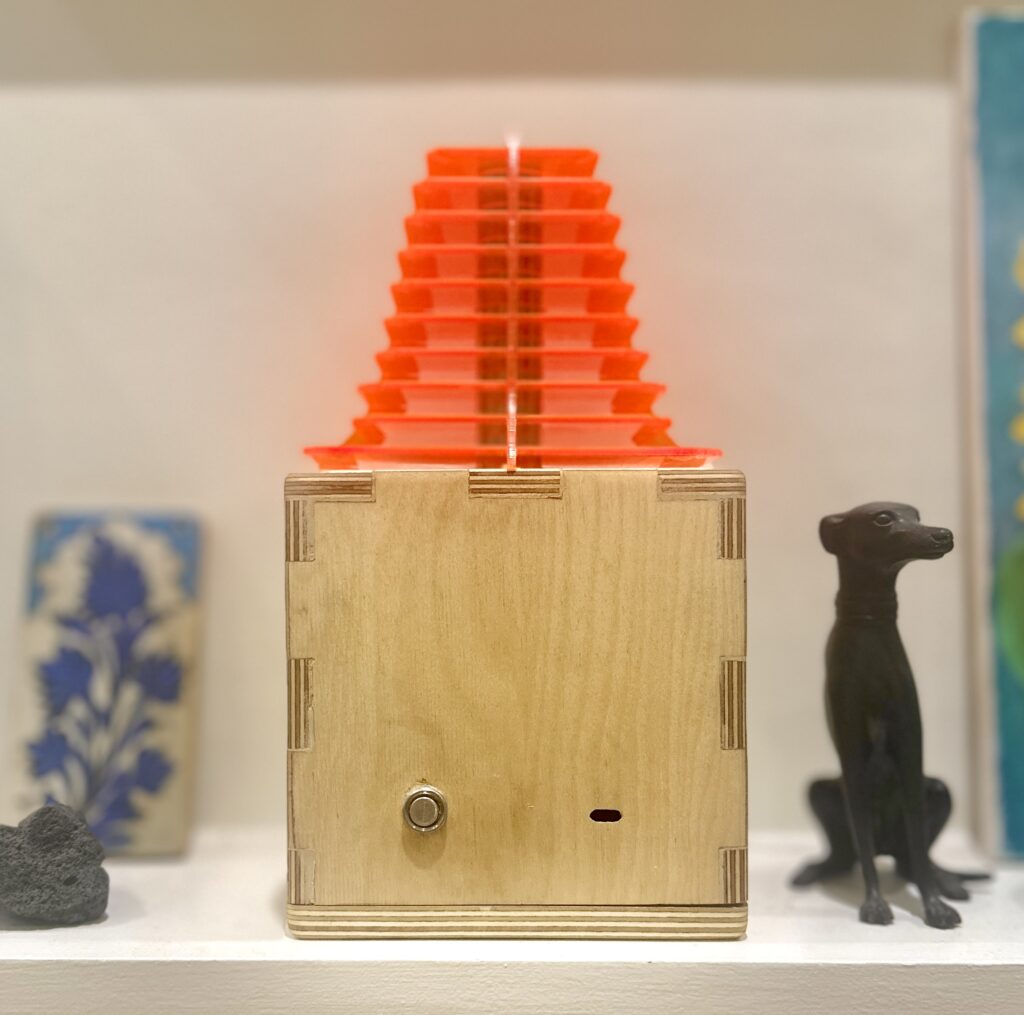
The final submitted coursework scored 94/100 and overall achieving the highest GCSE DT score in the history of the school (189/200).
All photos by me, capturing the journey from sketch to shine.
Leave a Reply